Overview
Ongoing research projects:
- Optimized nodes of hollow section structures subjected to fatigue loading
- DFG-TRR277-A06 funding period 2 - Laser-based powder bed fusion (LPBF) of steel elements for civil engineering - Basics of design and mechanical resilience
Completed research projects:
- DFG-TRR277-A06 funding period 1 - Laser-based powder bed fusion (LPBF) of steel elements for civil engineering - Basics of design and mechanical resilience
- Tensegrity knots for the deutsche Museum
Optimized nodes of hollow section structures subjected to fatigue loading

- DLR FOSTA Project
- Project period: 01.02.2025-01.02.2028
- Project partners: Chair of Structural Analysis (TUM), Institute for Materials and Construction Research - Laboratory for Steel and Light Metal Construction (Munich University of Applied Sciences)
Initial Position
- Hollow section structures are a widely used form of construction due to material efficiency and robustness.
- Nodes are welded or designed as steel castings. However, there are various difficulties with regard to manufacturing, dimensioning and especially fatigue.
- Alternatively, the nodes can be manufactured by laser metal deposition (Direct Energy Deposition, (DED)).
Steel productgroups/ steelgrades
- Round hollow sections made of S355 are connected with X-and K-nodes made of 316L stainless steel (1.4404).
Research aim
- Development of a scientific basis for the optimized design and construction of additively manufactured hollow profile nodes, taking into account manufacturing-specific boundary conditions.
- Use of additive manufacturing in combination with form finding to create nodes with a higher degree of complexity and much greater geometric freedom.
Benefits for the steel application
- Increased steel utilization through resource-efficient and innovative connection options.
- New business areas and increased competitiveness for Germany
People
DFG-TRR277-A06 funding period 2 - Laser-based powder bed fusion (LPBF) of steel elements for civil engineering - Basics of design and mechanical resilience
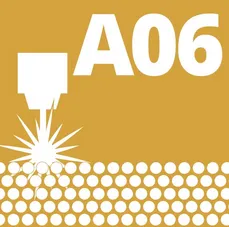
- DFG-TRR277-A06
- Project period: 2024-2028
- Project partners: Institut für Werkzeugmaschinen und Betriebswissenschaften (iwb), TUM
- Internetseite
The aim of this project is to identify and evaluate the key factors influencing the production of safe and durable steel components using laser-based powder bed fusion (LPBF). In particular, the relationship and dependencies between LPBF process, post-treatment and geometry with microstructure and mechanical properties are investigated and modeled.
Motivation:
LPBF is one of the key technologies among metal additive manufacturing processes. It makes it possible to produce highly complex structures very precisely directly from digital design data. As a result, the process is already being used in series production in many industrial sectors. Thanks to its properties, LPBF also offers great potential for the construction industry: Additive manufacturing could revolutionise the construction industry due to the high degree of design freedom, the direct link between the real and digital worlds and the cost-effectiveness of batch sizes of one. LPBF is particularly suitable for the production of elements for steel construction.
Project aims of 2 nd funding period
- Applying an additional material providing a higher yield strength than 316L while maintaining a high elongation at fracture
- Increased reliability through fatigue life prediction
- Tailored part properties by including lattice structures
- Recommendations for a processing route that guarantees reliable mechanical properties and a low ecologic impact
Methods
Transfer to a new material
- Static and dynamic material characterisation of a new manganese steel with higher strength and elongation at fracture than 316L
- Testing the transferability of results from the 1 st funding period to the new material
- Providing a processing route for the new material
Fatigue life prediction
- In-situ detection of pore formation during the manufacturing
- Methodology to obtain stress intensity factors for pores detected by process monitoring
- Calibration with mechanical simulations of µCT-scanned parts
Tailored part properties
- Inclusion of tailored lattice structures in LPBF parts
- Homogenised static material property model
- Integration into the design optimisation
Joints and connections
- Joining and testing of local and global structures
- Including fusion zone properties into design optimisation 0.5 mm 100 µm
Environmental sustainability
- Collecting comprehensive data for a life-cycle assessment
- Evaluation of the ecologic impacts of the LPBF processing steps
Outlook 3 rd funding period
- Further tailoring of LPBF parts to optimise the damping behaviour
- Process combination with directed energy deposition processes to increase the maximum scale of the manufactured parts
- Include environmental and ecological sustainability considerations (Life-Cycle Cost Analysis) in the digital design workflow of LPBF construction elements
Acknowledgement
This project has received funding from the German Research Foundation (DFG) as part of the SFB/ TRR 277 - Additive Manufacturing in Construction - The Opportunity of Large Impact (project number 414265976).
We would like to express our sincere thanks for this.
People
DFG-TRR277-A06 funding period 1 - Laser-based powder bed fusion (LPBF) of steel elements for civil engineering - fundamentals of design and mechanical strength
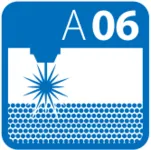
- DFG-TRR277-A06
- Project period: 2020-2024
- Projekt partners: Institut für Werkzeugmaschinen und Betriebswissenschaften (iwb), TUM
Project aims of 2 nd funding period
To date, it has not been possible to reliably predict and reproduce the mechanical properties of LPBF-manufactured steel elements. In order to establish the process in the construction industry, it is necessary to develop a methodology for the reliable production of durable steel construction elements using LPBF.
Methods
Firstly, the influence of process parameters on the cooling rates during LPBF will be analysed using in-process thermography. In addition, the influence of geometric aspects and post-treatments on the mechanical and metallurgical properties of the components will be analysed. In the further course of the project, shape-optimised steel components and large components will be produced with the help of the investigated relationships and tested under real operating conditions. Finally, a methodology will be derived that enables the economical and process-reliable use of LPBF in the construction industry.
Results
As part of this research project, the correlations between process parameters, cooling rates, post-treatment and geometric aspects with the static and cyclic mechanical properties of LPBF-manufactured steel components will be determined. Based on these findings, design recommendations will then be derived in order to manufacture steel components with reproducible and defined mechanical properties using LPBF.
Acknowledgement
This project has received funding from the German Research Foundation (DFG) as part of the SFB/ TRR 277 - Additive Manufacturing in Construction - The Opportunity of Large Impact (project number 414265976).
We would like to express our sincere thanks for this.
People
Christina Radlbeck, Johanes Diller, Rudolf Röß, Dorina Siebert
Tensegrity knots for the deutsche Museum
In the course of an industrial project with the Deutsches Museum in Munich, a tensegrity tower is to be developed and manufactured. For this purpose, additively manufactured connecting nodes are produced by means of shape optimization.
The shape optimization was carried out by the project partner C02 of TRR277.