Cutting Pattern Generation
Due to its influence on the bearing behaviour, geometry plays an important role in lightweight structures. The usage of doubly curved surfaces leads to extremely efficient structures and is therefore widely used in lightweight structures.
A doubly curved surface cannot be developed into a plane without compromises which result in additional residual stresses when the structure will be erected. In addition, the elastic deformation due to pre-stress has to be compensated.
Cutting pattern generation determines a plane and stress-free geometry. After erection, this geometry leads to a shape of equilibrium with a minimal deviation from the target structure.
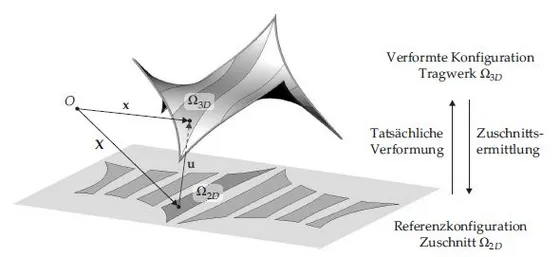
Cutting pattern generation is a key part of the design of membrane structures among a large variety of engineering disciplines, like the draping of fibre-reinforced plastics.
The Variation of Reference Strategy was developed for the cutting pattern generation of arbitrary materials. The method minimizes the potential which results out of the erection process and the pre-stress by varying the reference geometry.
Cutting Pattern Generation with Isogeometric Analysis
Isogeometric Analysis exactly represents complex geometries and uses them for analysis. Two advantages follow from this for the cutting pattern generation: in both pre- and postprocessing no dealing with meshes is necessary and no information is lost with respect to geometry. On the one hand, the meshing process is redundant before analysis and on the other hand, blueprint plans are directly available in CAD compatible data.
In order to benefit from this, elements for the Variation of Reference Strategy are developed within the framework of Isogeometric B-Rep Analysi
Links to our research activities in the field of Isogeometric Analysis
- Isogeometric Analysis
- Isogeometric B-Rep Analysis
- Integration of CAD and CAE
- Fibre-reinforced structures