Übersicht
Laufende Forschungsprojekte:
- Optimierte Knoten von ermüdungsbeanspruchten Hohlprofilkonstruktionen
- DFG-TRR277-A06 Förderphase 2 - Laser-Strahlschmelzen (LPBF) von Stahlelementen für das Bauwesen – Grundlagen der Konstruktion und der mechanischen Belastbarkeit
Abgeschlossene Forschungsprojekte:
- DFG-TRR277-A06 Förderphase 1 - Laser-Strahlschmelzen (LPBF) von Stahlelementen für das Bauwesen – Grundlagen der Konstruktion und der mechanischen Belastbarkeit
- Tensegrity Knoten für das deutsche Museum
Optimierte Knoten von ermüdungsbeanspruchten Hohlprofilkonstruktionen

- DLR FOSTA Projekt
- Projektzeitraum: 01.02.2025-01.02.2028
- Projektpartner: Lehrstuhl für Statik (TUM), Institut für Material-und Bauforschung - Labor für Stahl-und Leichtmetallbau (Hochschule München)
Ausgangslage
- Hohlprofilkonstruktionen sind aufgrund von Materialeffizienz und Robustheit eine weitverbreitete Konstruktionsform
- Knoten werden geschweißt oder als Stahlgussteile ausgeführt. Dabei gibt es allerdings diverse Schwierigkeiten bzgl. Fertigung, Bemessung und Ermüdung.
- Alternativ können die Knoten per Laser-Auftragsschweißen (engl. DirectedEnergy Deposition, (DED)) additiv gefertigt werden
Stahlproduktgruppen /Stahlsorten
- Runde Hohlprofile aus S355 werden mit additiv gefertigten X-undK-Knoten
aus dem Werkstoff 316L (1.4404) verbunden.
Forschungsziel
- Schaffung einer wissenschaftlichen Grundlage für den optimierten Entwurf und die Bemessung additiv gefertigter Hohlprofilknoten unter Berücksichtigung fertigungsspezifischer Randbedingungen
- Nutzung der additiven Fertigung in Kombination mit der Formfindung um Knoten mit höherem Komplexitätsgrad und wesentlich größerer geometrischer Freiheit zu schaffen.
Nutzen für die Stahlanwendung
- Gesteigerte Stahlanwendung durch ressourceneffiziente und innovative Anschlussmöglichkeiten
- Neue Geschäftsfelder und Steigerung der Wettbewerbsfähigkeit
Personen
TRR277 A06 Förderphase 2 – Laser-Strahlschmelzen (LPBF) von Stahlelementen für das Bauwesen – Grundlagen der Konstruktion und der mechanischen Belastbarkeit
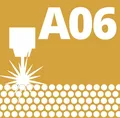
- DFG-TRR277-A06
- Projektzeitraum: 2024-2028
- Projektpartner: Institut für Werkzeugmaschinen und Betriebswissenschaften (iwb), TUM
- Internetseite
Ziel dieses Projekts ist die Erfassung und Bewertung der maßgebenden Einflussfaktoren auf die Fertigung von sicheren und langlebigen Stahlbauelementen mittels Laser-Strahlschmelzen (engl. laser-based powder bed fusion, kurz LPBF). Insbesondere werden der Zusammenhang und die Abhängigkeiten zwischen LPBF-Prozess, Nachbehandlung und Geometrie mit der Mikrostruktur und den mechanischen Eigenschaften untersucht und modelliert.
Motivation:
Das LPBF ist eine der Schlüsseltechnologien unter den metallischen additiven Fertigungsverfahren. Damit ist es möglich, hoch komplexe Strukturen sehr präzise direkt aus digitalen Konstruktionsdaten zu fertigen. Das hat dazu geführt, dass das Verfahren heute in vielen Industriebereichen bereits in der Serienfertigung eingesetzt wird. Durch seine Eigenschaften bietet das LPBF auch ein hohes Potenzial für das Bauwesen: Aufgrund der hohen Gestaltungsfreiheit, der direkten Verknüpfung von realer mit digitaler Welt und der Wirtschaftlichkeit bei Losgröße eins könnte die Additive Fertigung die Bauindustrie revolutionieren. Das LPBF eignet sich hierbei besonders für die Herstellung von Elementen für den Stahlbau.
Zielsetzung
- Applying an additional material providing a higher yield strength than 316L while maintaining a high elongation at fracture
- Increased reliability through fatigue life prediction
- Tailored part properties by including lattice structures
- Recommendations for a processing route that guarantees reliable mechanical properties and a low ecologic impact
- Erhöhte Zuverlässigkeit durch Vorhersage der Ermüdungslebensdauer
- Maßgeschneiderte Bauteileigenschaften durch Einbeziehung von Gitterstrukturen
- Empfehlungen für einen Verarbeitungsprozess, der zuverlässige mechanische Eigenschaften und geringe ökologische Auswirkungen garantiert
Vorgehen
Transfer to a new material
- Static and dynamic material characterisation of a new manganese steel with higher strength and elongation at fracture than 316L
- Testing the transferability of results from the 1 st funding period to the new material
- Providing a processing route for the new material
Fatigue life prediction
- In-situ detection of pore formation during the manufacturing
- Methodology to obtain stress intensity factors for pores detected by process monitoring
- Calibration with mechanical simulations of µCT-scanned parts
Tailored part properties
- Inclusion of tailored lattice structures in LPBF parts
- Homogenised static material property model
- Integration into the design optimisation
Joints and connections
- Joining and testing of local and global structures
- Including fusion zone properties into design optimisation 0.5 mm 100 µm
Environmental sustainability
- Collecting comprehensive data for a life-cycle assessment
- Evaluation of the ecologic impacts of the LPBF processing steps
Ausblick Förderphase 3
- Further tailoring of LPBF parts to optimise the damping behaviour
- Process combination with directed energy deposition processes to increase the maximum scale of the manufactured parts
- Include environmental and ecological sustainability considerations (Life-Cycle Cost Analysis) in the digital design workflow of LPBF construction elements
Danksagung
Dieses Projekt hat eine Finanzierung durch die Deutsche Forschungsgemeinschaft (DFG) im Rahmen des SFB/ TRR 277 – Additive Manufacturing in Construction – The Opportunity of Large Impact (Projektnummer 414265976) erhalten.
Hierfür möchten wir unseren größten Dank aussprechen.
Personen
TRR277 A06 Förderphase 1– Laser-Strahlschmelzen (LPBF) von Stahlelementen für das Bauwesen – Grundlagen der Konstruktion und der mechanischen Belastbarkeit
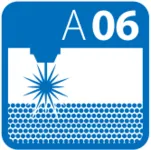
- DFG-TRR277-A06
- Projektzeitraum: 2020-2024
- Projektpartner: Institut für Werkzeugmaschinen und Betriebswissenschaften (iwb), TUM
Zielsetzung
Bisher ist eine zuverlässige Vorhersage und Reproduzierbarkeit der mechanischen Eigenschaften von LPBF-gefertigten Stahlelementen noch nicht möglich. Um das Verfahren im Bauwesen etablieren zu können, ist es notwendig, eine Methodik zur prozesssicheren Fertigung von langlebigen Stahlbauelementen mittels LPBF zu entwickeln.
Vorgehen
Zunächst wird mithilfe von In-Prozess-Thermographie der Einfluss von Prozessparametern auf die Abkühlraten beim LPBF untersucht. Zudem sollen die Einflüsse von geometrischen Aspekten und Nachbehandlungen auf die mechanischen und metallurgischen Eigenschaften der Bauteile untersucht werden. Im weiteren Verlauf des Projekts werden mithilfe der untersuchten Zusammenhänge, formoptimierte Stahlbauelemente und Großbauteile hergestellt und unter Berücksichtigung realer Einsatzbedingungen getestet. Abschließend soll eine Methodik abgeleitet werden, welche den wirtschaftlichen und prozesssichern Einsatz von LPBF im Bauwesen ermöglicht.
Ergebnisse
Im Rahmen dieses Forschungsprojekts werden die Zusammenhänge zwischen Prozess-parametern, Abkühlraten, Nachbehandlung und geometrischen Aspekten mit den statischen und zyklischen mechanischen Eigenschaften von LPBF-gefertigten Stahlbauteilen ermittelt. Basierend auf diesen Erkenntnissen sollen anschließend Konstruktionsempfehlungen abgeleitet werden, um Stahlbauteile mit reproduzierbaren und definierten mechanischen Eigenschaften mittels LPBF zu fertigen.
Danksagung
Dieses Projekt hat eine Finanzierung durch die Deutsche Forschungsgemeinschaft (DFG) im Rahmen des SFB/ TRR 277 – Additive Manufacturing in Construction – The Challenge of Large Scale (Projektnummer 414265976) erhalten.
Hierfür möchten wir unseren größten Dank aussprechen.
Personen
Christina Radlbeck, Johannes Diller, Rudolf Röß, Dorina Siebert